[ad_1]
Effective warehouse management is a crucial factor for successful sellers, ensuring timely deliveries and cost efficiency. However, achieving excellence in warehousing demands more than just wishful thinking. It necessitates a profound grasp of inventory control and a purposeful approach designed to optimize outcomes.
If you’ve grappled with cumbersome warehouse operations or aim to enhance your processes, our comprehensive guide is here to assist you. Within this resource, we delve into the foundational aspects of efficient warehouse management and provide valuable best practices for enhancing your warehousing operations.
What Is Warehouse Management?
If your business involves selling products, you likely require a designated space for storing inventory between orders, unless you operate as a dropshipping model. Typically, this storage takes place in a warehouse or a fulfillment center.
However, the process of handling inventory, from receiving stock to storing goods and fulfilling orders, can become chaotic without a well-organized warehouse. Inadequate warehouse management can lead to fulfillment delays, resulting in late, incorrect, or even undelivered orders to customers.
Warehouse management encompasses the systematic control and coordination of stock movements within your warehouse, ensuring a seamless flow of goods in and out. As a business grows, the complexities of inbound and outbound logistics can increase, but effective warehouse management simplifies and expedites these processes.
Also referred to as warehousing, warehouse management encompasses every facet of the order fulfillment journey. This includes activities such as inventory tracking, stock reception, storage, order picking, packing, and shipping. However, its scope extends beyond these operations.
Warehouse management strives to harmonize all the moving components of your warehouse, incorporating elements like staff training, inventory planning, workflow optimization, and performance monitoring. It allows businesses of all sizes to closely monitor their fulfillment processes, identify areas of concern, and implement necessary improvements without disrupting the flow of goods.
Efficient warehousing yields immediate benefits:
- Enhanced Customer Satisfaction: Although warehouse operations remain behind the scenes, they have a visible impact on the speed and accuracy of order delivery, leading to improved customer satisfaction.
- Cost Savings: A well-organized warehouse streamlines inventory management, making it easier to store, locate, retrieve, and ship products, thereby reducing labor costs and work hours.
- Streamlined Supply Chain: The positive effects of warehouse management resonate throughout the supply chain, ensuring quicker order processing, faster order fulfillment, and optimal utilization of warehouse space.
What Is a Warehouse Management System (WMS)?
As previously discussed, managing a warehouse is a significant endeavor that becomes increasingly intricate as businesses grow in size and pace. Consequently, to enable effective warehousing, companies often rely on Warehouse Management Systems (WMS).
A Warehouse Management System, often referred to as WMS, encompasses a suite of software and hardware tools designed to streamline warehouse operations. While some may call it warehouse management software or inventory management software, especially when used exclusively online, it essentially comprises tools that simplify the complexities of warehousing and order fulfillment.
WMS is frequently integrated into a broader Enterprise Resource Planning (ERP) suite, although it can also function as a standalone product dedicated to optimizing and simplifying warehouse management. WMS enhances your warehousing process in several ways, including:
- Providing real-time visibility into inventory levels and their respective locations.
- Harnessing data analytics and automation to predict demand and sales patterns.
- Utilizing artificial intelligence (AI) to devise and execute efficient daily operational plans.
- Offering precise instructions to guide staff through daily tasks, such as receiving and storing inventory, in accordance with predefined rules.
- Monitoring performance and delivering a comprehensive overview of operational health and potential issues.
In addition to its intrinsic value for warehousing, the prominence of WMS has surged, particularly in response to the escalating trends in e-commerce. Global e-commerce is projected to surpass a staggering $29 trillion in value by 2023. To meet this burgeoning demand, companies in the United States alone are anticipated to expand their warehouse space by over 1 billion square feet by 2025.
WMS plays a pivotal role in enabling companies to effectively scale their warehouse operations in tandem with growing demand. Furthermore, it’s noteworthy that as e-commerce flourishes, customer expectations regarding delivery lead times continue to shorten.
People increasingly desire faster deliveries, and companies can only meet this expectation by leveraging high-quality WMS solutions.
The Warehouse Management Process in Five Key Steps
Warehouse management is a vital component of supply chain management, and its intricacies can vary depending on the nature of the products a business deals with. For instance, companies handling perishable goods will adopt different strategies compared to those dealing with durable products.
Similarly, manufacturing firms will implement distinct storage and handling procedures compared to trading companies.
Despite these variations, warehouse management universally aims to achieve specific core objectives, which include the following:
- Inventory Tracking: Inventory tracking involves continuous monitoring and updating of stock levels. It is crucial for businesses to maintain a clear understanding of available inventory within the warehouse, its exact location, and when replenishment is required. This process ensures complete visibility into the state of inventory, aids in supervising supplies from vendors, and facilitates demand forecasting.
- Receiving and Stowing: Efficient reception and storage of incoming goods are essential components of the warehouse management process. In an optimized system, goods move seamlessly from trucks at loading docks, where they are scanned, to designated storage areas such as pallets, shelves, or freezers. Delays or confusion in the placement of items can create bottlenecks, underscoring the importance of clear instructions and handheld screens for warehouse staff.
- Picking and Packing: Picking refers to the retrieval of ordered items when customer orders are received. Various tactics are employed to minimize effort and expedite this process, such as zone picking, discrete picking, wave picking, and batch picking. Once picked, the next step is packing, which can vary in complexity depending on the products. Efficiency is maintained through organized systems and checklists to ensure order accuracy.
- Shipping: Shipping represents the final stage of order fulfillment, where the objective is to deliver the order to the customer. Shipping can introduce complexities related to costs, distances, and maintaining the integrity of the shipped items. Proper packing that considers item characteristics, such as waterproof packaging for wet goods and cool packaging for frozen products, is essential. An efficient order tracking system and a user-friendly interface for order status updates are also crucial.
- Reporting: After orders have been packed, shipped, and successfully delivered, it is essential to conduct a comprehensive review. This involves updating inventory status after outgoings and generating reports on key performance indicators (KPIs). Warehouse management software is often used to enhance transparency related to KPIs. It records returns, identifies error causes, and helps minimize errors in fulfillment operations.
It is important to note that each of these warehouse processes is interconnected. Effective planning and execution in each step contribute to overall process efficiency, ensuring smoother operations and improved outcomes.
The 11 Warehouse Management Best Practices
After exploring the fundamentals of warehouse management and its processes, it’s time to delve into effective warehousing best practices. Here are eleven valuable tips for enhancing warehouse management that you can implement today:
- Warehouse Management System (WMS): Utilize WMS tools to streamline warehouse operations, optimize space, and reduce labor costs. WMS adoption is on the rise, with 85% of warehouse operations incorporating it into their processes. Robotics and AI are also emerging trends in 2022, reflecting a shift toward smart inventory management.
- Cloud Storage: Consider moving your warehouse operations to the cloud to benefit from advantages like data storage, accessibility, and cost savings. Cloud computing eliminates concerns about on-premises data storage and the need for dedicated IT teams.
- Data Collection Technology: Implement data collection technologies such as barcodes, RFID, and SKUs for automated recording of inbound and outbound stock. These technologies enhance visibility, accuracy, and efficiency while reducing the risk of human errors.
- Automation: Automate various warehouse processes to improve speed and accuracy. This includes automating stock storage, retrieval, and packing processes. Robotics and conveyor systems can also expedite item picking and delivery.
- Hands-Free Picking: Enable hands-free picking with automated systems, making it easier for workers to retrieve items using wrist-mounted or handheld radio frequency units. This reduces physical labor, improves turnaround time, and increases warehouse throughput.
- Wave Planning: Implement wave planning to optimize picking routes and reduce picking time and effort. Wave planning is particularly beneficial for small businesses, combining discrete picking with efficient tactics.
- Touch Minimization: Minimize excessive handling of goods to reduce the risk of damage or mishandling. This practice increases process integrity and accelerates fulfillment by eliminating redundant retrieval and shelf return.
- Cycle Counting: Complement WMS with manual cycle counting to verify inventory accuracy. Instead of single-day counts, implement cycle counting to break up the counting process and maintain accurate stock levels.
- Warehouse Safety: Prioritize worker safety by providing necessary safety equipment and health measures. Ensuring a safe working environment prevents injuries that can disrupt operations.
- Standardized Vendor Operations: Efficiently manage supplier coordination, including delivery times, delivery forms, and delivery locations. Streamlining these factors ensures a consistent supply of goods when needed.
- Daily Health Check: Conduct regular, in-depth health checks to assess the state of warehouse operations against KPIs. Identify deviations from the plan and take appropriate actions to optimize processes, add new steps, or remove bottlenecks.
By implementing these best practices, you can enhance the efficiency and effectiveness of your warehouse management, ultimately improving overall operations.
Discover Sturdy and Secure Warehouses on Alibaba.com
In summary, effective warehouse management offers optimal avenues to fulfill customer requirements and guarantee complete satisfaction. When coupled with contemporary technology, the implementation of warehousing best practices equips your business with the means to expand and capture increased sales while catering to a growing customer clientele.
If you are in search of robust warehousing solutions, Alibaba.com offers an extensive seller directory where you can access top-tier suppliers offering competitive prices. Initiate a seller account today to commence your search.
Contact us for more details now
Related articles:
[ad_2]
Article link
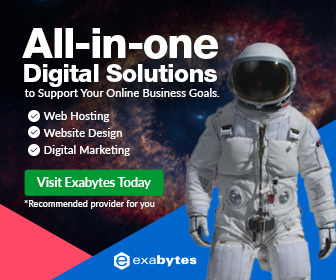